Thomas Tomski, Vice President End Users at Emerson explores the problems caused by climate change in the Cold Chain and the best ways they can be solved
Over the past few decades, a lot of progress has been made towards more sustainable food production. However, meeting the UN Global Development Goals and reducing emissions remains a major climate challenge. A significant part of addressing this challenge is through the cold chain – the preservation of our food supply from farm to fork.
Earlier this month I discussed the topic in detail with the British Retail Consortium and a manager of refrigeration engineering for Waitrose, part of the John Lewis Partnership. The webinar discussion was focused on supporting food retailers with sustainable refrigeration – as the industry relies heavily on the cold chain and is arguably hit the hardest by F-gas regulation.
As anyone working in the cold chain is well aware, F-gas regulation has taken refrigeration from behind the scenes to the top of retail managers’ agendas. Hydrofluorocarbons (HFC), a greenhouse gas that has historically been used in most cold chain refrigerants, is being phased down at a rapid pace across Europe and around the world. In Europe, the HFC supply will be reduced by 40% this year compared to 2015 levels, meaning businesses need to swiftly replace their cooling systems or else face costly coolant shortages.
It also means that business managers need to carefully assess their options of new sustainable technologies that are being developed.
Three Refrigeration Architectures
At Emerson, we’ve identified three different types of refrigeration system architectures that are all able to deliver future-proof refrigeration solutions, but meet different customer and market needs. These include centralised boosters, integral display cases including waterloop systems, and decentralised condensing units.
So far, it would seem most businesses phasing out HFCs are opting for CO2 booster systems, a solution that does help reduce the global warming potential of refrigerants, however has more of a complex architecture that is more demanding in design, operation and maintenance. Integral display case systems such as “waterloop hydrocarbon integrals” have seen less uptake, however represent several potential benefits including simpler installation and less maintenance, improved operation, and less prone to efficiency degradation in warmer climates. The third option of a decentralised condensing unit adds another layer of flexibility and is starting to become more popular in some markets due to ease of commissioning and set-up in new stores.
We have made significant investments in developing solutions for these system architectures and have undertaken extensive studies with third party institutes and end customers in order to verify the benefits.
But how does a business ensure they select the best long-term solution?
When it comes to assessing technologies, businesses have traditionally focused on the broad categories of investment cost, operating costs and lately, compliance and sustainability. However when considering a cooling system, more specific factors might be overlooked such as revenue impact of facility layouts (e.g. whether refrigeration systems can be moved easily), to re-modelling frequency, investment in installation skills, and maintenance costs. This is why businesses updating their refrigeration systems need to take what I call a Total Cost of Ownership approach.
To put it simply, it means broadening traditional assessment parameters for new technologies to include more specific questions. For example a business should consider if everyone across their existing supply base – including contractors, consultants, installers, service engineers – is set up to service a refrigeration system across their regional markets. This question has a lot to do with the available skill levels for design, operating and service of systems.
Taking a Total Cost of Ownership approach also helps ensure businesses tackle as much of the climate change challenge as possible. For example, while replacing HFCs reduces environmental impact, it only tackles part of the problem: 75% of cooling emissions come from energy consumption rather than refrigeration leaks.
Ultimately, parameters for identifying a refrigeration system are very individual and businesses will come to different conclusions about which technology is right for them. But, it is important to go through a comprehensive process in order to avoid the risk of rushing into a stop-gap solution that only addresses one aspect of the sustainability challenge.
Emerson has boldly transformed itself to create value for our customers and shareholders. With our newly energized focus on our two core business platforms — Automation Solutions and Commercial & Residential Solutions — we can confront the challenges of an increasingly complex and unpredictable marketplace from a position of strength. This allows us to drive both near- and long-term value. And retain our single-trusted-partner status with the process, industrial, commercial and residential industries.
For more information on the HFC phase-down and refrigeration strategies, you can see our webinar with the BRC and Waitrose. Emerson also has a number of resources including online webinars and design expertise, to help those in the commercial refrigeration industry understand the implications of the F-gas regulation and the long-term solutions available online at https://climate.emerson.com/en-gb.
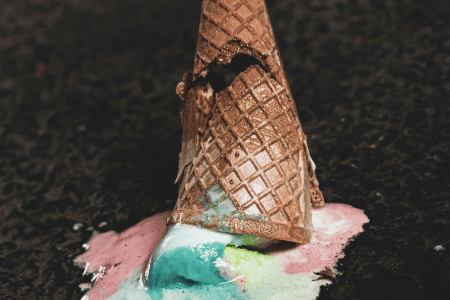